31.01.2025г
Предисловие
В настоящем документе, в дополнение к документу «Двигатель авиационны поршневой 2ДП 8,2/6,5х2. Обоснование принятых конструктивных решений», показана технология создания двигателя внутреннего сгорания. Большее место уделено рабочему циклу – единственному источнику энергии тепловой машины, которой является поршневой ДВС, и динамике. Эти два комплекса процессов являются первоисточниками всех нагрузок в двигателе и определяют его конструкцию, энергетические, экономические и массогабаритные характеристики. Их оптимизация – ключевая задача разработчика.
Согласно ГОСТ 2.120-2013, текущая стадия – технический проект, отчет с расчетами не предъявляется. Но расчеты выполнены, без них невозможно проектирование. Они включают, помимо названных выше: прочность деталей и сборок, шлицевые и шпоночные соединения, зубчатые передачи, подшипники, посадки, насосы, пружины и пр. Всё это вещи рутинные, понятные каждому инженеру, поэтому здесь представлены фрагментами.
На базе расчетов выпущен полный комплект чертежной конструкторской документации на изготовление макета-демонстратора двигателя для ОКР и доводки.
Поскольку технического задания на проектирование нет (составить ТЗ с потенциальными заказчиками не удалось, несмотря на неоднократные письменные обращения), мощность двигателя задана предполагаемо востребованным диапазоном 100-200 л.с. Проведенный анализ характеристик продаваемых на мировом рынке АПД, легший в основу выбора концепции, изложен в документе, упомянутом выше.
При обеспечении проекта необходимым экспериментальным оборудованием и ресурсами, разработчик гарантирует доводку двигателя до согласованных параметров ТЗ, когда оно появится. Гарантией являются личные компетенции разработчика, обретенные в многолетней работе на моторостроительном предприятии АО «Волгоградский моторный завод» в должности начальника конструкторского бюро, также в последующей разработке двигателей энергетической и авиационной специализации. Компетенции заключаются в обладании технологией создания ДВС, включающей проведение расчетов, выпуск конструкторской документации, создание исследовательских методик, проведение НИОКР.
Подтверждением сказанному является то, что все расчеты, графика и аналитика по настоящему проекту выполнены разработчиком, без привлечения сторонних специалистов.
Примечание. В конструкции двигателя есть патентоспособные решения, не имеющие в настоящее время защиты, поэтому в графическом материале и описаниях такие решения не отражаются.
Содержание
1. Рабочий цикл двигателя, тепловые и газодинамические расчеты
1.1. Предварительные расчеты рабочего цикла
1.2. Профилирование каналов газообменного тракта, статическая продувка
1.3. Модель и ее параметры для расчета рабочего цикла
1.4. Результаты расчета рабочего цикла, прогноз эффективных параметров
1.4.1. Критерии сходимости расчетов
1.4.2. Рассчитанные параметры цикла, тепловой баланс
1.4.3. Определение доли потерянного при продувке топлива
1.4.4. Оценка количества остаточных газов
1.4.5. Расчет прогнозируемых эффективных параметров двигателя
1.5. Данные для проектирования системы охлаждения
1.6. Выбор теплоносителя системы охлаждения
1.7. Визуализация продувки и воспламенения
1.8. Графики результатов расчетов
2. Динамический расчет двигателя
2.1. Данные динамического моделирования для прочностных расчетов двигателя
2.2. Динамическое моделирование работы демпфера винта
3.1. Диаграммы износа шеек коленчатого вала
3.2. Расчет элемента сборного корпуса двигателя
3.3. Расчет шатуна и шатунных болтов
4. Последовательность доводки двигателя
1. Рабочий цикл двигателя, тепловые и газодинамические расчеты
Цель работ, представленных в данном разделе – создание рабочего цикла двигателя, традиционно называемого рабочим процессом. Энергия цикла является источником полезной работы двигателя (для чего он и создается), но также и всех первичных термических, механических и динамических нагрузок в его конструкции.
Увеличение полезной работы и минимизация нагрузок являются главными критериями при создании рабочего цикла. Давления и температуры в цилиндре двигателя и характер их изменения являются задающими данными для расчетов динамических характеристик двигателя, прочности его деталей, расчета системы охлаждения, и, в значительной степени, определяют конструкцию двигателя.
На текущем этапе проекта задано внешнее смесеобразование, что существенно усложняет задачу достижения высоких экономических показателей.
В принятой конструктивной схеме двигателя – с противоположно движущимися поршнями (ПДП), типичное смесеобразование – непосредственная подача топлива в цилиндр, который предварительно очищается от отработавших газов чистым воздухом, нагнетаемым с избытком. После закрытия выпускных окон подается топливо. Задача газообмена решается относительно просто.
Непосредственная подача топлива в цилиндр планируется в дальнейшем развитии двигателя. На текущем этапе задан наиболее простой и дешевый в изготовлении и эксплуатации вариант – с внешним смесеобразованием.
При внешнем смесеобразовании продувка осуществляется не воздухом, а топливовоздушной смесью. При этом происходит смешивание смеси с отработавшими газами и ухудшение ее качества. Смешивание начинается с момента открытия продувочных окон (заброс отработавших газов из цилиндра во впускную трассу, т.к. давление в цилиндре выше), и далее, при вытеснении отработавших газов. В случае полной продувки цилиндра часть рабочей смеси попадает в выпускную трассу, теряется, что приводит к повышению расхода топлива.
Оптимальным решением является минимизация смешивания газов, что достигается через конструкцию окон и газообменных трасс (формы, направления и сечения окон, объемы и сечения трасс), и организация неполной, но достаточной продувки цилиндра, что достигается выбором наилучшей комбинации группы факторов конструктивного и регулировочного характера.
1.1. Предварительные расчеты рабочего цикла
Предварительные расчеты рабочего цикла двигателя являются первым, совместным с выбором конструктивных параметров, этапом создания любого ДВС.
Расчеты производились с помощью программы Волгоградского государственного политехнического института (описана в источнике: Математическое моделирование рабочих процессов ДВС: Учебное пособие / А.В. Васильев, Е.А.Григорьев; Волгоград. гос. техн. ун-т. – Волгоград, 2002. - 67 с.). Программа создавалась, дорабатывалась и успешно применялась КБ рабочего процесса в 1990-х годах для разработки и доводки 4-х тактных двигателей АО «Волгоградский моторный завод».
В программе «..используется гипотеза полного перемешивания: поступающий в цилиндр воздух … образует однородную смесь с находящимися там газами. Состояние этой смеси квазиравновесно: в каждой точке объёма цилиндра в данный момент времени температура, давление и концентрация компонентов одинаковы» (цитата из источника).
Указанное свойство – «полное перемешивание», при расчете газообмена 2-х тактного двигателя ПДП, не позволяет определить потерю рабочей смеси и параметры рабочего тела при продувке, поэтому разработчиком настоящего проекта программа была дополнена. Дополнение позволяет считать входящий и исходящий газы в цилиндре разделенными границей и не смешивающимися. Такое допущение дает более адекватную картину в цилиндре в конце газообмена, но, естественно, содержит непрогнозируемую ошибку, т.к. реального движения потоков, определяющегося конфигурацией газообменных каналов и ряда других факторов, не учитывает. Тем не менее, доработка программы позволила получить первичные исходные данные для проектирования и расчетов двигателя.
Расчеты рабочего цикла с использованием дополненной программы выполнены с условием недопущения потерь топлива при продувке, что контролировалось через коэффициент избытка продувочного воздуха (верхняя граница – 0,95). Расчет, с одной стороны, имитировал наиболее экономичный вариант смесеобразования – с непосредственным впрыском топлива, с другой – создавал основу для применения варианта с внешним смесеобразованием с минимальными потерями топлива при продувке.
После компоновочного проектирования двигателя на базе предварительных расчетов проведена разработка и оптимизация газообменного тракта и процесса сгорания. Для этого использовались программные продукты ANSYS Fluent и ANSYS Forte. Моделировался двигатель с внешним смесеобразованием (Причины выбора данного варианта описаны в документе «Двигатель авиационный поршневой 2ДП 8,2/6,5х2. Обоснование принятых конструктивных решений»).
Оптимизация была проведена до достижения уровня удельного расхода топлива, декларируемого для двигателя ROTAX 915 iS.
Причина остановки дальнейшей оптимизации – высокая трудоемкость работ с комплексами ANSYS Fluent и ANSYS Forte в связи с отсутствием у разработчика специализированного аппаратного обеспечения.
1.2. Профилирование каналов газообменного тракта, статическая продувка
Данный этап являлся подготовительным перед решением задачи в динамической постановке. Цель этапа - снижение трудоемкости разработки профиля окон цилиндра.
Поставленная задача: спроектировать профиль окон, обеспечивающих наиболее полное вытеснение отработавших газов при их минимальном смешивании со свежим зарядом.
Использованный программный продукт – ANSYS Fluent.
Визуализация статической продувки тракта с одним из вариантов профилей продувочных и выпускных окон представлен на рис.1.
Рисунок 1
Визуализация статической продувки тракта
Пояснения к рисунку:
- Показана продувка первого (определяемого по ГОСТ Р 53461 – 2009) цилиндра.
- Положение цилиндра на рисунке: продувочные каналы находятся в нижней части, выпускные – в верхней.
По результатам этапа определены конфигурация и параметры газообменных окон цилиндра, отвечающие в первом приближении поставленным требованиям.
1.3. Модель и ее параметры для расчета рабочего цикла
Следующий этап – оптимизация газообмена, смесеобразования и сгорания в динамической постановке задачи на 3D модели.
В расчетах использовался программный продукт – ANSYS Forte.
Параметры модели задавались на основе конструкции проектируемого двигателя, анализа прототипов и опыта разработчика.
В качестве двигателя для сравнения выбран ROTAX 915 iS (см. «Двигатель авиационный поршневой 2ДП 8,2/6,5х2. Обоснование принятых конструктивных решений»).
Данные ROTAX 915 iS (источник - https://ru.wikibrief.org/wiki/Rotax_915_iS):
- диаметр цилиндра: 84,0 мм;
- ход поршня: 61,0 мм;
- количество цилиндров: 4;
- рабочий объем: 1352 куб. см;
Комплектация:
- турбокомпрессор со степенью наддува на сравниваемом режиме 3,5: 1;
- тип топлива: высокооктановый автомобильный бензин;
- системы охлаждения: жидкостная и воздушная;
- редуктор: зубчатая передача.
Эффективные параметры:
- выходная мощность: 101 кВт (135 л.с.), продолжительная;
- удельный расход топлива: 280 - 310 г /кВт/ч при частоте вращения коленвала 5500 об/мин;
Примечание. Двигатель ROTAX 915 iS имеет в составе системы газообмена ТКР и ОНВ. Применение их в проектируемом двигателе существенно улучшило бы его эффективные параметры, но на первом этапе ставится задача достигнуть целевые показатели в максимально простой комплектации, только с продувочным компрессором с механическим приводом. Влияние ТКР и ОНВ будет оценено в результатах расчета дополнительно.
Задаваемые значения для моделирования двигателя 2ДП 82/65х2:
- конструктивные:
· диаметр цилиндра: 82,0 мм;
· ход поршня: 2 х 65,0 мм;
· количество цилиндров: 2;
· рабочий объем 1373 куб. см;
· степень сжатия действительная: 8,0;
· продувка: центробежным компрессором с механическим приводом от коленчатого вала, подача воздуха задается массовым расходом;
· моделирование производится с полным объемом газовоздушных трасс – от соединения с патрубком продувочного компрессора до выходного соединения выпускного коллектора;
- параметры расчета:
· частота вращения коленчатого вала: 5500 об/мин;
· целевая индикаторная мощность одного цилиндра (пересчет от ROTAX 915 iS с условно заданным механическим КПД = 0,85): 59,4 кВт;
· смесеобразование: карбюраторное, подача стехиометрической горючей смеси;
· коэффициент избытка воздуха: 1,0;
· топливо: изооктан, низшая теплотворная способность 44 МДж/кг;
· стехиометрическое отношение: 15,028:1;
· параметры окружающей среды: T=288,15 К, P=0,1013 МПа;
· период расчета – 360 град. п.к.в., начиная с угла открытия выпускных окон первого цилиндра;
· внутрицилиндровые процессы рассчитываются только в первом цилиндре;
· воспламенение – от одной свечи, имитация отказа второй свечи;
- температуры поверхностей теплообмена:
· внутренняя поверхность цилиндра: 175 °С;
· огневая поверхность впускного поршня: 300 °С;
· поверхность тронка впускного поршня: 160 °С;
· огневая поверхность выпускного поршня: 350 °С;
· поверхность тронка выпускного поршня: 200 °С;
· поверхности выпускной трассы: 200 °С;
· поверхности продувочной трассы: 50 °С.
Примечание. Температуры поверхностей теплообмена в принятой модели расчета задавались единым средним значением для каждой поверхности. При их назначении акцент делался на моделирование теплообмена наиболее термически нагруженных участков. Влияние температур на триботехнические условия работы пары цилиндр-поршень не учитывалось.
Принятые упрощения модели:
- уплотнение поршней производится по плоскости огневой поверхности;
- открытие/закрытие окон производится кромкой огневой поверхности поршней;
- зазор поршень – цилиндр отсутствует;
- утечки рабочего тела в картерное пространство отсутствуют;
- кромки окон, поршней, внутренних поверхностей трасс газообмена не имеют скруглений и фасок.
Критерии сходимости расчетов:
В качестве критериев устоявшегося режима при расчетах принято условие допустимого расхождения значений в контрольных точках для следующих параметров:
· давление в цилиндре в начальной точке и через 360 град. п.к.в.;
· температура в цилиндре в начальной точке и через 360 град. п.к.в.;
· масса газов в цилиндре в начале и конце газообмена;
· разница масс вошедшего и вышедшего газов в цилиндре;
· разница масс вошедшего в цилиндр и половины поданного в продувочную трассу газа;
· отклонение от заданного циклового расхода.
ЗD модель газообменного тракта
Модель газообменного тракта представляет собой внутреннюю полость коробов продувки и выпуска с подводящими трубопроводами, имитацию гильзы цилиндра, объемные профили выпускных и продувочных окон с геометрическим расположением, соответствующем конструкции двигателя, и имитацию огневой поверхности и тронка поршней. Закон перемещения поршней и их фазовое смещение заданы программно, в соответствии с длиной шатуна и центровкой поршневого пальца.
Рисунок 2
3D модель газообменного тракта
1.4. Результаты расчета рабочего цикла, прогноз эффективных параметров
Проведена серия расчетов рабочего цикла двигателя, во время которой конструктивно дорабатывались параметры окон цилиндра и других элементов газовоздушного тракта с целью уменьшения потерь топлива при продувке, снижения средней температуры газов в цилиндре, снижения давления газов во впускном коллекторе и, соответственно, снижения затрат мощности на привод продувочного компрессора.
Далее проведена серия расчетов регулировочных характеристик с целью оптимизации характеристики выгорания топлива, скорости нарастания давления (жесткости процесса), минимизации максимальных значений температур и давлений цикла.
Результаты оптимизации в цифровой и графической (рис. 3-17) форме представлены в следующих разделах.
1.4.1. Критерии сходимости расчетов
Получены следующие расхождения значений в контрольных точках:
· давление в цилиндре: 1,07% при угле открытия выпускных окон;
· температура в цилиндре: 0,67% при угле открытия выпускных окон;
· масса газов в начале и конце газообмена: 0,64% - при угле открытия выпускных и угле закрытия продувочных окон;
· разница масс вошедшего и вышедшего газов: -0,22% - при угле открытия выпускных и угле закрытия продувочных окон;
· разница масс вошедшего и 1/2 поданного во впускной коллектор газа: -0,22%;
· отклонение от заданного циклового расхода: 0,77%.
Значения контрольных параметров приняты как подтверждающие сходимость.
1.4.2. Рассчитанные параметры цикла, тепловой баланс
Получены следующие за рабочий цикл одного цилиндра значения:
· масса рабочего тела в цилиндре после продувки: 0,7145 г;
· цикловой расход топлива*: 0,0418 г;
· среднее расчетное давление во впускном коллекторе: 0,2077 МПа;
· химическое тепловыделение при сгорании топлива: 1666 Дж;
· полнота химического сгорания поданного за цикл топлива*: 0,906;
· полнота химического сгорания топлива, находящегося в цилиндре: 0,977;
· индикаторная работа: 670.4 Дж, 40% от химического тепловыделения;
· потери энергии на теплопередачу в стенки: 244 Дж, 15% от химического тепловыделения;
· потери энергии с отработавшими газами: 7519 Дж, 45% от химического тепловыделения;
· коэффициент замещения продувочным агентом: 0,955;
· индикаторная мощность: 61,46 кВт;
· индикаторный расход топлива*: 224,5 г/кВт/ч;
· среднее индикаторное давление: 0,977 МПа;
· индикаторный КПД*: 0,365;
· максимальное давление цикла: 6,70 МПа;
· максимальная температура цикла: 2714 К;
· максимальная скорость нарастания давления: 0,433 МПа/град.
Примечание. * В расчетах параметра учитывается всё топливо, вошедшее в цилиндр, в том числе потерянное при продувке.
При расчетах оределялись регулировочные характеристики по углу опережения зажигания с одной и двумя свечами. При умеренно уменьшенном угле опережения зажигания цикл отличается меньшими максимальным давлением, температурой и жесткостью при некотором снижении мощности и ухудшении экономичности:
· индикаторная мощность: 61,15 кВт;
· индикаторный расход топлива*: 227,7 г/кВт/ч;
· среднее индикаторное давление: 0,972 МПа;
· индикаторный КПД*: 0,363;
· максимальное давление цикла: 5,96 МПа;
· максимальная температура цикла: 2667 К;
· максимальная скорость нарастания давления: 0,306 МПа/град.
Моделирование с зажиганием двумя свечами показывает более быстрое сгорание, некоторое улучшение мощностных и экономических показателей при росте максимальных давлений, температур и жесткости.
1.4.3. Определение доли потерянного при продувке топлива
Масса топлива, участвовавшая в сгорании в цилиндре, вычисляется как отношения:
(химическое тепловыделение при сгорании топлива) / (полнота химического сгорания топлива, находящегося в цилиндре) / (низшая теплотворная способность топлива)
и составляет:
1666 / 0,977 / 44000 = 0,0388 (г)
откуда масса потерянного топлива:
0,0418 - 0,0388 = 0,003 (г) или 7,2%
1.4.4. Оценка количества остаточных газов
Из определенной в п. 1.4.3 массы топлива в цилиндре и стехиометрического соотношения, указанного в разделе «Параметры для моделирования двигателя 2ДП 8,2/6,5х2», вычисляем действительное количество свежего заряда:
0,0388 * (15,028+1) = 0,6219 (г)
Вычитая из рабочей смеси, остающейся в цилиндре после газообмена, массу свежего заряда, определенную выше, получаем массу остаточных газов:
0,7145 – 0,6219 = 0,0926 (г)
откуда коэффициент остаточных газов: 0,13.
1.4.5. Расчет прогнозируемых эффективных параметров двигателя
Определение прогнозируемых эффективных показателей двигателя выполнено по вышеприведенным результатам расчета рабочего цикла и расчетов по п. 1.1, включавших предварительное определение производительности системы охлаждения и затрат мощности на ее привод, также других механических потерь.
Использованные данные предварительных расчетов по п. 1.1.
1) мощность трения поршневых комплектов: 7,2 кВт;
2) мощность трения в кривошипной и шатунной группе: 3,5 кВт;
3) мощность, расходуемая на привод гидронасосов смазки и охлаждения: 1,5 кВт;
4) потери в силовом редукторе при КПД=0,95: 5,0 кВт.
Итого, механические потери двигателя: 17,2 кВт.
Механический КПД двигателя без учета привода продувочного компрессора:
ηм = (61,46*2-17,2) / (61,46*2) = 0,862
Таблица 1
Результаты расчета затрат мощности на привод продувочного компрессора с πк=2,05
№ | Параметр | Ед. изм. | Значение |
1 | Подача компрессора | кг/с | 0,1203 |
2 | Давление на входе в компрессор | МПа | 0,1013 |
3 | Температура на входе в компрессор | К | 288,15 |
4 | Показатель адиабаты воздуха | - | 1,4 |
5 | Политропа сжатия в компрессоре | - | 1,55 |
6 | Степень повышения давления в продувочном компрессоре, πк | - | 2,05 |
7 | Давление на выходе из компрессора (соответствует среднему во впускном коллекторе) | МПа | 0,2077 |
8 | КПД компрессора политропный | - | 0,805 |
9 | Располагаемая работа политропного сжатия | Дж | 67 628 |
10 | КПД привода компрессора механический | - | 0,95 |
11 | Мощность на привод продувочного компрессора, Nпк | кВт | 10,63 |
Прогнозируемые
эффективные параметры двигателя с продувочным компрессором с приводом от
коленчатого вала:
Ne = Ni * ηм – Nпк = 61,46*2* 0,86 – 10,63 = 95,1 кВт (129,3 л.с.)
ge = 290,2 г/кВт/ч (213,4 г/л.с./ч)
При применении в конструкции двигателя дополнительно в качестве ступени наддува ТКР, степень повышения давления продувочным компрессором может быть снижена не менее чем до 1,16 единиц, что приведет к существенному уменьшению затрат на его привод. При условии сохранения циклового расхода топлива (для сопоставимости расчетов), для достижения необходимого давления продувки и компенсации увеличившегося противодавления в выпускном коллекторе, необходимая степень повышения давления ТКР будет ориентировочно 1,8. Эффективная мощность двигателя увеличится на величину уменьшения затрат мощности на привод продувочного компрессора. При этом несколько увеличатся давление и температура цикла. Прогнозируемые результаты представлены ниже.
Таблица 2
Результаты расчета затрат мощности на привод продувочного компрессора с πк=1,16
№ | Параметр | Ед. изм. | Значение |
1 | Подача компрессора | кг/с | 0,1203 |
2 | Давление на входе в компрессор | МПа | 0,1823 |
3 | Температура на входе в компрессор | К | 374,14 |
4 | Показатель адиабаты воздуха | - | 1,4 |
5 | Политропа сжатия в компрессоре | - | 1,55 |
6 | Степень повышения давления в продувочном компрессоре, πк | - | 1,16 |
7 | Давление на выходе из компрессора (соответствует среднему во впускном коллекторе) | МПа | 0,2115 |
8 | КПД компрессора политропный | - | 0,805 |
9 | Располагаемая работа политропного сжатия | Дж | 15 525 |
10 | КПД привода компрессора механический | - | 0,95 |
11 | Мощность на привод продувочного компрессора, Nпк | кВт | 2,44 |
Прогнозируемые
эффективные параметры двигателя с продувочным компрессором с приводом от
коленчатого вала и ТКР:
Ne = Ni * ηм – Nпк = 61,46*2* 0,86 – 2,44 = 103,3 кВт (140,5 л.с.)
ge = 267,2 г/кВт/ч (196,5 г/л.с./ч)
Для снижения удельного расхода топлива возможно дополнительное применение ОНВ, в том числе и при одноступенчатом наддуве.
1.5. Данные для проектирования системы охлаждения
Средняя мощность теплового потока (рис. 13) из внутрицилиндрового пространства суммарно составила 22,183 кВт на 1 цилиндр, распределившись между поверхностями теплообмена следующим образом:
- поверхность цилиндра: 9,817 кВт (44,3%);
- огневая поверхность выпускного поршня: 6,121 кВт (27,6%);
- огневая поверхность впускного поршня: 6,246 кВт (28,2%).
Меньший теплоотвод выпускного поршня относительно впускного предположительно обусловлен:
- шатровой структурой истекающего потока и его ограниченным контактом с центральной зоной огневой поверхности поршня – рис. 3, также отражается в графике коэффициентов усреднённой по поверхности конвективной теплопередачи (рис.14);
- подачей "холодного" свежего заряда в центральную зону огневой поверхности выпускного поршня, что приводит к уменьшению отводимого теплового потока. Одновременно нагревающийся при этом контакте свежий заряд увеличивает свой удельный объем, что дополнительно минимизирует его потери в выпускную трассу (рис. 3 е-м);
- более высокой заданной в расчете температурой его огневой поверхности (350 °С по сравнению с впускным поршнем 300 °С), из чего следует уменьшение температурного напора и, соответственно, теплового потока при нахождении поршня в центральной зоне цилиндра, где температуры принимают максимальные значения (рис.13).
- потенциальным несоответствием назначенной температуры огневой поверхности поршней, фактически имевшейся бы в цикле.
По выпускному поршню, исходя из графиков мощности теплового потока (рис. 13), коэффициентов усреднённой по поверхности конвективной теплопередачи (рис.14), температурного напора на огневой поверхности поршня (рис.15) и выводов относительно структуры омывающего поршень потока, можно заключить, что наибольшее тепловое воздействие приходится на кромки днища поршня. Общее воздействие температур на всю поверхность днища в течение сжатия и расширения дополняется концентрированным воздействием на кромки в начале газообмена, длительность которого можно оценить в 110-120 град., где наиболее активны первые после открытия выпускных окон 30-40 град.
У впускного поршня также есть активный период теплообмена во время продувки, но, в отличие от выпускного поршня, в этот период идет отвод тепла от поршня и подогрев свежего заряда. В области максимальных значений температур газов в цилиндре отвод тепла в выпускной поршень выше, чем у выпускного, за счет большего температурного напора, обусловленного меньшей, чем у выпускного поршня, температурой огневой поверхности.
Для оценки зональной тепловой нагрузки цилиндра, по его продольной координате, между положениями огневых поверхностей выпускного и впускного поршней в наружных мертвых точках, определены мощности тепловых потоков (рис.16), максимальные температуры (рис.17) и продолжительность контакта газов (рис.18).
Граница внутренних кромок выпускных окон находится в районе координаты 55 мм, граница внутренних кромок продувочных окон находится в районе координаты -60 мм, положение в наружных мертвых точках огневой поверхности выпускного и впускного поршней соответственно 72 мм и -72 мм от центра цилиндра.
Таблица 3
Распределение тепловых потоков в цилиндре
Зона цилиндра | Продувка | Центр | Выпуск |
Координаты зоны, мм | -72 …-8 | -7 … 7 | 8 … 72 |
Мощность потока, Вт | 2471 | 4407 | 2967 |
Доля потока | 25% | 45% | 30% |
Из графиков на рис. 16-18 можно сделать вывод, что, в сравнении с газораспределительными узлами 4-х тактных двигателей, у двигателя ПДП газообменные окна подвергаются значительно меньшим термическим нагрузкам как по величине воздействующих температур, так и по времени этого воздействия.
1.6. Выбор теплоносителя системы охлаждения
Касательно выбора теплоносителя охлаждения цилиндров. Поршни охлаждаются маслом. Дополнительно к этому следует добавить в систему охлаждения, использующую масло в качестве хладагента, тепло смазочного масла от кривошипно-шатунных механизмов, трения цилиндро-поршневой группы, механических приводов гидросистемы и продувочного компрессора, синхронизирующей (одновременно являющейся редуктором винта) шестеренной передачи, демпфирующей муфты и подшипниковых узлов выходного вала (всего порядка 17 кВт потерь, конвертируемых в тепло, п. 4.1.5). Некоторая часть этого тепла будет отведена через конвективный теплообмен внешних стенок корпусов и трубопроводов, но большая уйдет в систему охлаждения. Таким образом, тепло, отводимое от цилиндров, составит в общем тепловом балансе системы охлаждения порядка 1/3.
Отсюда следует вывод, что система охлаждения де-факто является масляной. Поэтому охлаждение цилиндров также, если это возможно, следует осуществлять маслом.
Замечание. Очевидно, что принятая упрощенная модель расчета цикла не в полной мере описывает тепловые процессы и требует проверки натурными испытаниями. Тем не менее, характер изменения рассчитанных тепловых потоков дает достаточно информации для использования полученных данных в проектировании системы охлаждения.
1.7. Визуализация продувки и воспламенения
На рис. 3 и 4 представлены этапы продувки цилиндра и развитие процесса сгорания. Угол отсчитывается от внутренней мертвой точки выпускного поршня.
Рисунок 3
Диаграмма температур в продольном сечении цилиндра, на огневой поверхности выпускного поршня и верхних внутренних поверхностях коллекторов при продувке цилиндра и сжатии
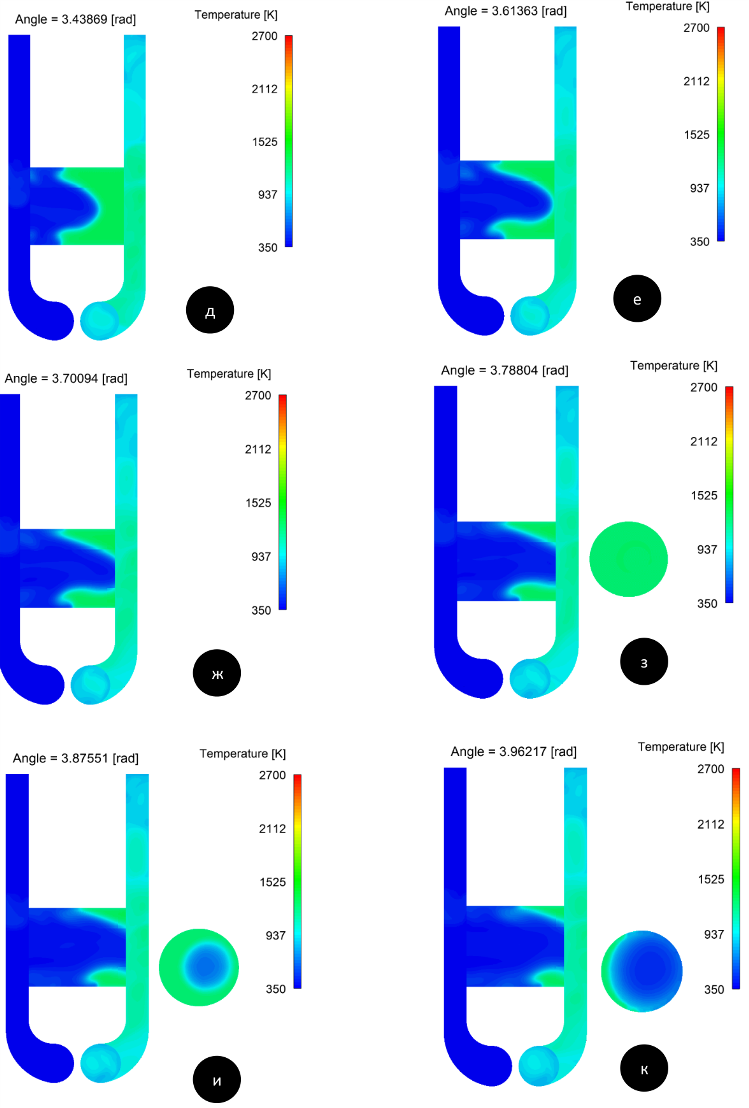
Рисунок
3, продолжение
Диаграмма температур в продольном сечении цилиндра, на огневой поверхности выпускного поршня и верхних внутренних поверхностях коллекторов при продувке цилиндра и сжатии
Рисунок 3, окончание
Диаграмма температур в продольном сечении цилиндра, на огневой поверхности выпускного поршня и верхних внутренних поверхностях коллекторов при продувке цилиндра и сжатии
Рисунок 4.
Диаграмма температур в центральном диаметральном и продольном
сечении цилиндра при воспламенении и развитии сгорания
1.8. Графики результатов расчетов
Рисунок 5
Рисунок 6
Рисунок 7
Рисунок 8
Рисунок 9
Рисунок 10
Рисунок 11
Рисунок 12
Рисунок 13
Рисунок 14
Рисунок 15
Рисунок 16
Рисунок 17
Рисунок 18
2. Динамический расчет двигателя
Целью динамических расчетов являются: конструктивная балансировка двигателя и его деталей, снижение внутренних и опорных динамических нагрузок от комбинации газовых и инерционных сил и выходного крутящего момента для всех рабочих режимов, получение данных для прочностных расчетов конструкции.
Динамическое моделирование проводилось с использованием программных продуктов ANSYS Motion и RecurDyn. Зубчатая передача силового редуктора моделировалась средствами программного комплекса KISSsoft.
Для нагружения поршней модели двигателя газовыми силами использовались результаты вычислений по п.1. «Рабочий цикл двигателя, тепловые и газодинамические расчеты».
Инерционные характеристики внешней нагрузки задавались посредством назначения выходному фланцу массы и момента инерции.
Исследовались варианты работы двигателя с балансирной электрической машиной (проверка работоспособности демпфера винта при испытаниях на стенде) и воздушным тормозом (мулинеткой), имитирующим винт, применяемый с двигателем ROTAX с редукторами типа «С» и «Е». Осевое усилие от винта не задавалось.
Демпфер винта моделировался в 2-х вариантах – пружинный скручивания (исключает осевую колебательную составляющую) и кулачковый типа применяемого в авиационных двигателях ROTAX. Расчеты показали сопоставимую эффективность обоих вариантов.
Динамическая модель двигателя включала нагрузки от присоединенных агрегатов – продувочного компрессора и блоков гидронасосов.
Вращающиеся и движущиеся детали модели по массогабаритным и инерционным характеристикам соответствовали проектным данным.
Адекватность модели как колебательной системы, прежде всего для создания условий работы демпфирующей муфты, обеспечивалась отсутствием прямого задания частот вращения деталей. Вывод модели на нужный скоростной режим, при жестко заданных нагружающих моментах, осуществлялся аналогично реальному двигателю, воздействием на характеристики давления в цилиндре. С целью сохранения максимальных значений давления газов неизменными (исключение фактора вариативности газовых нагрузок в комплексе изменяющихся других воздействий) коррекция работы газов осуществлялась смещением диаграммы относительно ВМТ. Во всех расчетах угол коррекции после стабилизации режима составлял менее 1 град. п.к.в.
Управление регулированием осуществлялось разработанной функцией – ПИД-регулятором, посредством блока RecurDyn CoLink.
Моделирование выполнено для работы двигателя в диапазоне мощностей от 100 л.с. до 200 л.с. при частоте вращения nк/в=5500 об/мин и для критических режимов, включая максимальный холостой ход при N=0, n=5800 об/мин при h=8000 м (с максимальными инерционными и минимальными газовыми силами).
Параллельно динамическому моделированию, по получаемым данным, проводились прочностные расчеты коленчатого вала, поршня, шатуна, зубчатой передачи, элементов силовой конструкции корпуса двигателя. По результатам прочностных расчетов вносились изменения в конструкцию деталей и динамическую модель, моделирование повторялось.
Дополнительно было проведено моделирование силового редуктора с передачей момента зубчатыми ремнями, поскольку такой вариант конструкции двигателя также прорабатывался. Виды расчетных моделей представлены на рис. 19, 20.
Рисунок 19
Модель двигателя с шестерённой передачей
Рисунок 20
Модель двигателя с ременной зубчатой передачей
В настоящем документе представлены 3 примера расчета.
2.1. Данные динамического моделирования для прочностных расчетов двигателя
Представлены результаты моделирования работы двигателя с максимальной расчетной мощностью. Режим характеризуется наибольшими газовыми нагрузками.
Параметры моделирования:
- мощность на выходном валу: Ne=200 л.с.;
- частота вращения коленчатых валов: nк/в=5500 об/мин;
- высота над уровнем моря: h=0 м.
Комплектация двигателя:
- коленчатые валы с противовесами полного динамического уравновешивания вращающихся масс кривошипно-шатунного механизма, включая вращающиеся части массы шатунов. Противовесы рассчитаны для полного устранения динамического моментного дисбаланса двигателя;
- нагружение – имитация винта (мулинетка, без осевого усилия) для редукторов типа «С» и «Е» двигателей ROTAX;
- демпфер винта кулачкового типа;
- редуктор шестеренного типа.
Результаты моделирования использованы в приведенных далее прочностных расчетах шатуна и шатунных болтов, поршневого комплекта и «выпускного» коленвала.
Рисунок 21
Данные моделирования динамики КШМ для прочностного расчета поршня
2.2. Динамическое моделирование работы демпфера винта
Параметры моделирования и комплектация двигателя – как в разделе 2.1.
Цель моделирования – подбор характеристик демпфера для работы с мулинеткой.
Моделировался также вариант работы двигателя с испытательным стендом (здесь не представлен). Инерционные характеристики ротора нагружающей машины стенда существенно отличаются от характеристик мулинетки. При подготовке двигателя к испытаниям указанный факт следует учитывать.
Результаты представлены графиками на рис. 22 и 23.
Пояснения к графикам:
- Ось абсцисс – в градусах поворота «выпускного» коленчатого вала.
- Представлен один поворот выходного вала (соответствует 862 град. п.к.в., передаточное отношение редуктора – 0,418).
Рисунок 22
График угловой скорости колеса редуктора и выходного вала
Рисунок 23
График крутящих моментов колеса редуктора и выходного вала
2.3. Сравнительная оценка виброактивности двигателя при использовании коленчатых валов с противовесами и без противовесов
Целью настоящего расчетного исследования является определение вибрационных характеристик двигателя в 2-х крайних (по влиянию на вибрации) комплектациях:
1) с коленчатыми валами с противовесами полного динамического уравновешивания вращающихся масс кривошипно-шатунного механизма;
2) с коленчатыми валами без противовесов.
Коленчатые валы по варианту 2 наименее технологически сложны и материалоемки, их применение уменьшает вес двигателя на 2,655 кг.
Условия моделирования: двигатель установлен на опорах через упругие изоляторы на фундамент. Точки измерения (расчета) вибрации - геометрический центр области контакта опоры с изолятором. Координаты центров условных опор показаны на рис. 24-25. Направления осей – согласно рис. 19: X – поперечная, Y – вертикальная, Z – продольная.
Параметры упругих изоляторов не оптимизировались (нет ТЗ на двигатель), для обоих вариантов моделирования заданы следующими характеристиками:
- жесткость по всем осям 1000 Н/мм;
- демпфирование по всем осям 10 Н*с/мм;
- предварительное нагружение (затяжка) отсутствует.
Параметры моделирования и комплектация двигателя, кроме коленчатых валов, соответствуют заданным в п.2.1.
Исследуется вибрация от вынужденных колебаний, вызываемых силами инерции движущихся деталей двигателя и крутильными колебаниями от неравномерности крутящего момента на выходном валу двигателя. Последние связаны с инерционной характеристикой нагружающего устройства. Оцениваемые параметры вибрации – среднее квадратическое значение (СКЗ) виброперемещений и виброскоростей по осям X, Y, Z.
Результаты моделирования представлены на графиках рис. 26-37 и в таблицах 4 и 5.
Пояснения к графикам:
- на графиках комплектация двигателя коленчатыми валами с противовесами обозначается сплошными линиями, без противовесов – пунктирными;
- ось абсцисс задана диапазоном 3000 град. – 3360 град. и соответствует одному повороту коленчатого вала.
Сравнительная оценка и замечания.
1) При использовании коленчатого вала без противовесов увеличилась виброактивность двигателя по всем осям, в большей степени в направлениях осей Y и Z, что связано с возникновением моментного дисбаланса от несбалансированных вращающихся масс шатунных шеек коленчатых валов и части массы закрепленных на них шатунов, относимых к вращающимся совместно с шейками.
2) Решение о применении варианта коленчатого вала будет определяться ТЗ.
3) В анализе не оценивались изменения внутренних нагрузок в двигателе и их влияние на прочность и ресурс. Предварительные расчеты показывают некритичность этого влияния, но, в случае возможности выбора, предпочтение следует отдать коленчатому валу с противовесами.
4) При доводке двигателя и/или при проектировании его на меньшую мощность, массы подвижных деталей могут быть уменьшены. Соответственно, снизятся вызываемые ими инерционные силы и виброактивность.
5) Применение в составе наддува ТКР (при монтаже его на двигатель) увеличит вес двигателя и его инерционные характеристики, что приведут к снижению виброактивности двигателя в обеих комплектациях.
6) Возможен вариант конструкции коленчатого вала с противовесами неполной компенсации дисбаланса, что также уменьшит вибрации при меньшем росте массы.
Таблица 4
СКЗ виброперемещений, мкм
Таблица 5
СКЗ виброскорости, мм/с
Рисунок 24
Расположение точек измерения вибрации двигателя. Вид спереди
Рисунок 25
Расположение точек измерения вибрации двигателя, вид сверху
Рисунок 26
График виброскорости по оси X на опоре Vp_1
Рисунок 27
График виброскорости по оси X на опоре Vp_2
Рисунок 28
График виброскорости по оси X на опоре Vip_1
Рисунок 29
График виброскорости по оси X на опоре Vip_2
Рисунок 30
График виброскорости по оси Y на опоре Vp_1
Рисунок 31
График виброскорости по оси Y на опоре Vp_2
Рисунок 32
График виброскорости оси Y на опоре Vip_1
Рисунок 33
График виброскорости по оси Y на опоре Vip_2
Рисунок 34
График виброскорости по оси Z на опоре Vp_1
Рисунок 35
График виброскорости по оси Z на опоре Vp_2
Рисунок 36
График виброскорости по оси Z на опоре Vip_1
Рисунок 37
График виброскорости по оси Z на опоре Vip_2
3. Выдержки из расчетов
По данным, полученным при расчетах рабочего цикла двигателя п.1. «Рабочий процесс двигателя, тепловые и газодинамические расчеты» и динамических расчетах п.2. «Динамический расчет двигателя», произведены прочностные расчеты деталей и узлов двигателя.
Несколько выдержек из расчетов представлено ниже. Материалы, условия, пространственные и относительные положения взаимодействующих деталей в двигателе на момент расчета и результаты расчетов, а также методики расчетов, не приводятся.
В расчетах использованы программные продукты комплекса ANSYS и Mathcad Prime.
3.1. Диаграммы износа шеек коленчатого вала
По данным динамических расчетов двигателя построены безразмерные диаграммы износа коренных и шатунных шеек коленчатых валов. Диаграммы показывают интенсивность нагружения различных зон шеек и используются для выбора места подвода масла в шейках коленчатого вала.
Пояснения к диаграммам:
- сплошная линия – шатунная шейка «впускного» коленчатого вала;
- пунктирная линия – шатунная шейка «выпускного» коленчатого вала;
- угловое положение 0 - шейка в НМТ, вращение против часовой стрелки;
- шкала износа – условная.
3.2. Расчет элемента сборного корпуса двигателя
Усилия между впускным и выпускным картерами корпуса двигателя определяются газовыми и инерционными силами от поршневых комплектов и шатунов.
По данным проведенных динамических расчетов в диапазоне возможных режимов работы двигателя, усилия между картерами всегда являются растягивающими и достигают максимального значения 39400 Н на режиме максимальных холостых оборотов: Ne=0, nк/в=5800 об/мин при h= 8000 м.
Деталями, обеспечивающими силовое замыкание корпуса двигателя между картерами, являются корпус редуктора и плита соединительная.
В связи с тем, что имеющиеся вычислительные мощности не позволили определить распределение сил между корпусом редуктора и плитой соединительной в динамической модели, оценка прочности соединения произведена определением коэффициента запаса прочности при статическом нагружении на разрыв детали с наименьшим сечением в нагруженной зоне – плиты соединительной. Прикладываемое усилие – полная разрывающая сила между картерами: 39400 Н.
При площади сечения 790 мм2 получаем напряжение 49,9 МПа, что в 4,9 раза меньше предела пропорциональности (245 МПа) дюралюминиевого сплава Д16Т.
Рисунок 40
Режим максимальных холостых оборотов: Ne=0, nк/в=5800 об/мин при h= 8000 м
3.3. Расчет шатуна и шатунных болтов
На рис. 41 представлена 3D модель сборного шатуна двигателя с массой и инерционными характеристиками, на рис. 42 и 43 – модель шатуна с поршневым пальцем и шатунной шейкой коленвала, нагруженная силами с целью определения напряжений в деталях сборки и оптимизации момента затяжки болтов.
По данным динамического расчета максимальная нагрузка на шатун составила:
- на растяжение 6600 Н, режим Ne=0, nк/в=5800 об/мин при h=8000 м. Для проверочного расчета принимается 10000 Н;
- на сжатие 29300 Н, режим Ne=200 л.с., nк/в =5500 об/мин при h=0. Для проверочного расчета принимается 30000 Н.
Рисунок 41
Масса и инерционные характеристики шатуна
В конструкции шатуна в качестве шатунного болта на начальном этапе используется стандартное изделие Болт со звездообразной головкой ГОСТ Р 52854 – В М6 х 60 – 10.9.
Характеристики прочности болта – в соответствии с ГОСТ.
Момент затяжки болта – 6 Нм.
Рисунок 42
Растяжение 10000Н
Рисунок 43
Сжатие 30000Н
3.4. Расчет коленчатого вала
На рис. 44 представлен графический результат расчета на прочность «выпускного» коленчатого вала в варианте полной уравновешенности вращающихся масс кривошипно-шатунного механизма.
Данные для расчета получены из теплового расчета и динамической модели.
Режим: Ne=200 л.с., nк/в =5500 об/мин при h=0.
Коленчатый вал нагружен моментами привода винта, привода продувочного компрессора, привода маслонасосов смазки и охлаждения.
Расчет произведен для положения с наиболее тяжелой комбинацией сил от шатунно-поршневых групп.
Угловая скорость в точке расчета 577 рад/с, угловое ускорение -19360 рад/с.Рисунок 44
Расчет коленчатого вала на прочность
3.5. Расчет поршня
На рис. 45 представлен вариант расчета на прочность «выпускного» поршневого комплекта в сборе, без компрессионных и маслосъемного колец.
Данные для расчета получены из теплового расчета и динамической модели.
Условия расчета:
Режим: Ne=200 л.с., nк/в =5500 об/мин при h=0.
Ускорение 12317 м/с2.
Давление газов 7,569 МПа.
Температура деталей поршневого комплекта от 100 до 250 С°.
Рисунок 45
Расчет поршневого комплекта на прочность
4. Доводка двигателя
Исходя из собственного опыта, первичная доводка макета двигателя 2ДП 8,2/6,5х2 до ресурса 500 – 1000 м/ч может быть произведена в течение 6 – 12 месяцев чистого времени работы при условии укомплектования необходимой исследовательской аппаратурой и оперативного изготовления экспериментальных деталей и нестандартного оборудования.
Указанные сроки исполнимы для постоянной мощности 130-140 л.с. при 5500 об/мин и карбюраторном смесеобразовании, т.к. для этого режима произведен уточненный расчет рабочего цикла, оптимизированы фазы газообмена и профили окон цилиндра (см. раздел 1. Рабочий цикл двигателя, тепловые и газодинамические расчеты).
Переход на другой режим или другую систему смесеобразования потребует дополнительное время.
Прочность основных деталей двигателя и производительность его систем смазки и охлаждения рассчитывались на мощность 200 л.с. при 5500 об/мин, поэтому, кроме производительности систем, которые, скорее всего, придется уменьшать, коррекции не предвидятся.
Укрупненно первичная доводка будет включать:
- оптимизацию профиля и размеров поршня;
- корректировку производительности систем воздухоподачи, смазки, охлаждения, откачки, оптимизацию их проточных и разгрузочных частей;
- доводку силового редуктора, выбора варианта демпфера винта и оптимизацию его параметров, доводку узла в целом, после чего корпус редуктора верхний сборный может быть заменен на литой, учитывающий окончательный вариант демпфера винта. Литой вариант облегчит и упростит конструкцию корпуса редуктора.
При подготовке двигателя к производству, в зависимости от серии, может быть целесообразен переход на литые конструкции всех корпусных деталей, что облегчит вес двигателя и значительно уменьшит количество операций механической обработки.
Достаточная для первого запуска, нагружения и первичной доводки комплектация стендового оборудования – согласно ГОСТ 14846-2020 «Двигатели автомобильные. Методы стендовых испытаний», п. 7 «Испытательный стенд и аппаратура» с динамометром (нагружающее устройство) типа мотор-генератор (балансирная машина), без оборудования для измерения дымности и токсичности.
Требуемое дополнительное нестандартное оборудование:
1) Насосные станции с регулируемой подачей для:
- системы смазки и охлаждения поршней – 2 шт. Каждый тракт должен быть обеспечен маслоочисткой и измерением расхода, давления и температуры на входе в картер (чертежи на механическую часть с интегрированным фильтром разработаны);
- системы охлаждения цилиндра – 1 шт. (оптимизация гидравлического тракта системы охлаждения цилиндров). Тракт должен быть обеспечен маслоочисткой, измерением давления и температуры на входе в цилиндры и выходе из них (2 выхода), измерением расходов на выходах (чертежи на механическую часть с интегрированным фильтром разработаны);
- системы откачки масла из картеров – 2 шт. с расходомерами и измерением температуры на выходе из картера (чертежи на механическую часть разработаны).
2) Компрессорный агрегат с центробежным нагнетателем управляемой подачи и расходомером воздуха для системы продувки и наддува (чертежи на механическую часть разработаны).
Исследовательское оборудование должно обязательно включать индицирующий комплекс для доводки рабочего цикла двигателя.
В дальнейшем, с целью ускорения и удешевления работ, для:
- перехода на непосредственный или распределенный в зону цилиндра впрыск;
- оптимизацию охлаждения цилиндра;
- оптимизацию охлаждения поршня;
- оптимизацию работы пары трения цилиндр-поршень;
- снижения расхода масла на угар;
- форсирования цикла,
потребуется изготовление исследовательской одноцилиндровой установки (ОЦУ) с комплектацией ее дополнительным нестандартным оборудованием, перечисленным выше.
Подробно о необходимости ОЦУ – в документе «Двигатель авиационный поршневой 2ДП 8,2/6,5х2. Обоснование принятых конструктивных решений. п.8. ОЦУ для доводки рабочего процесса и систем двигателя».
Для проекта двигателя 2ДП 8,2/6,5х2 ОЦУ разработана.